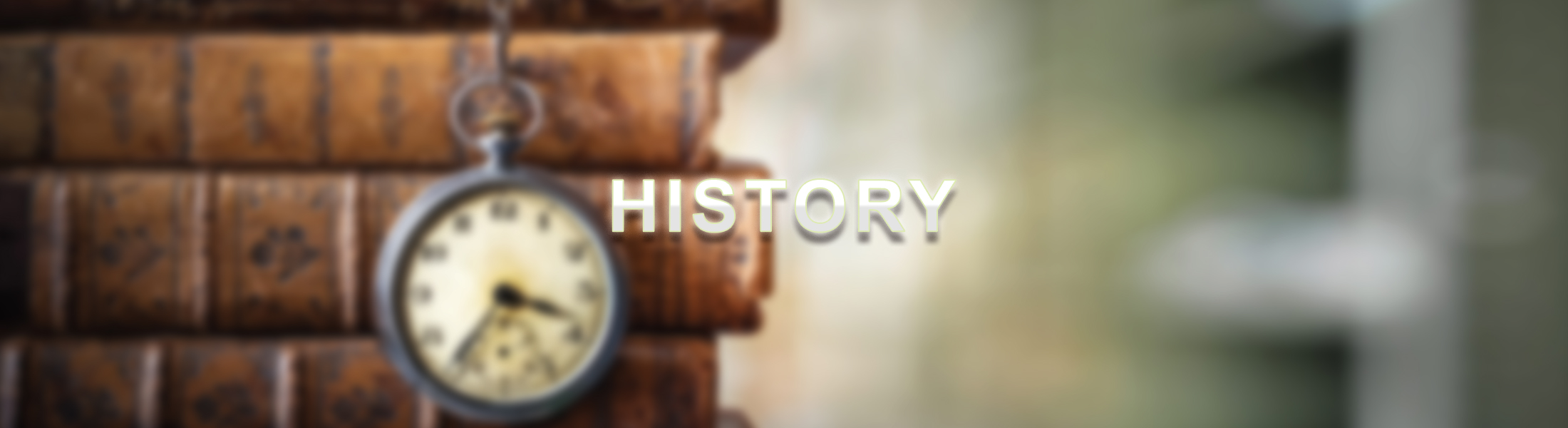
1975
Established a hydraulic cylinder manufacturing facility for the heavy equipment industry.
1980
Pioneered the development and manufacture of fully automatic waste oil heating furnaces. As a result, thousands of automotive service garages throughout Canada and the United States were able to use recovered oil to heat their facilities.
1987
Manufactured the first high capacity automatic oil filter briquetter. The machine is designed to crush multiple filters into a dense brick while extracting up to 98% of the oil in the process. The filter brick became the first processed filter output to be accepted as a recyclable product at North American smelters. Numerous installations are operational throughout Canada and the United States.
1990
Won an international competition to develop and install a prototype machine to process filters and metal cans for use on US Naval warships. This was a significant environmental “win” as previously this waste was dumped at sea.
1997
Created a specialized heavy duty briquetter to process oil filters and cans at recycling centres contained within military bases.
1998
Developed a briquetter capable of processing the coolant-laden metal chips and turnings created during the machining process at automotive and aerospace manufacturing facilities. The technology recovered 98% of the coolant/cutting fluids and creates a dense metal briquette with significant additional scrap value. These briquetters are operational at facilities throughout North America.
1999
Pioneered the development of an automatic briquetter to process off-spec full food cans. Thousands of metal cans and the food they contained could be recycled as opposed to being sent to area landfills.
2000
Designed and implemented the first super high density briquetter capable of producing furnace-ready briquettes from metal fines such as cast iron. Large automotive parts suppliers still currently use these durable machines on a 24/7 basis.
2002
Designed, manufactured and delivered the first high capacity, fully automatic hazardous waste processor for full or partially full aerosol and paint cans. Cans are compacted into dense briquettes and the liquids and gases are automatically separated for recycling or further processing.
2004
Released an upgraded aerosol/paint can/propane cylinder processor that achieved a “Best Available Technology” designation in the United Kingdom. The technologies’ ability to capture the propellant for recycling was the key to the success of the technology. Large units are operating in Europe, Australia, and the United States.
2006
Developed specialized handling equipment for the nuclear waste industry. Units are operational in Canada and South Korea.
2009
Designed a high capacity heavy duty briquetter capable of converting tire wire into a valuable commodity. Previously, this wire was considered a low or even no-value ugly byproduct of the used tire recycling process. Units are operational in Europe and North America.
2010
Designed BioKrushTM – the first super high-capacity industrial sized biomass briquetter. It is designed to convert vast amounts of various bio-energy sources into premium bio-fuel briquettes for use as a replacement for conventional fossil fuels. Our BioKrush™ technology now allows facilities with significant fuel needs to reduce their carbon footprint and make use of a promising, effective, renewable fuel resource.